Mining operations are tough on equipment. The heavy machinery used in excavation, crushing, and material transport must endure extreme pressure, high loads, dust, and harsh environmental conditions. Without proper lubrication, these machines can quickly suffer from wear and tear, leading to costly repairs, downtime, and inefficiencies.
At Rackers Equipment Company, we know that lubrication is one of the most critical maintenance factors in keeping mining equipment operating efficiently. Let’s explore why it’s important, how it protects your investment, and best practices for effective lubrication.
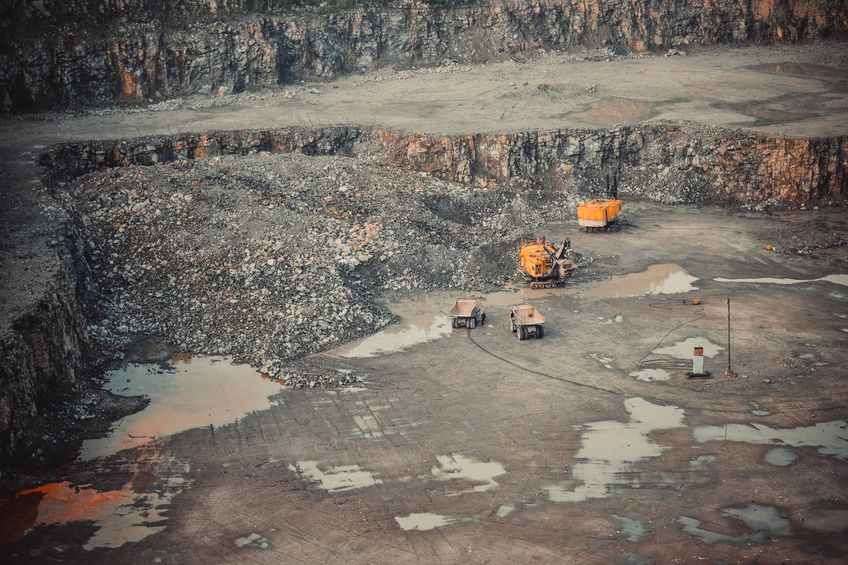
Why Lubrication Matters in Mining Equipment
Every piece of mining equipment—from crushers to loaders—has moving parts that require constant lubrication to function properly. Here’s why lubrication is essential:
1. Reducing Friction and Wear – The constant movement of metal components can lead to friction, which generates heat and accelerates wear. Lubricants create a protective layer between surfaces, reducing direct metal-to-metal contact and preventing premature failure.
2. Preventing Overheating – Mining machinery operates under extreme loads, causing components to heat up quickly. The right lubricant helps dissipate heat, keeping equipment cool and preventing thermal damage.
3. Protecting Against Contaminants – Dust, dirt, water, and debris are everywhere in a mining environment. Lubricants act as a barrier, keeping contaminants out of sensitive components and reducing the risk of corrosion and damage.
4. Enhancing Equipment Longevity – Without proper lubrication, essential components like bearings, gears, and hydraulic systems can wear out quickly. By reducing strain and wear, lubrication extends the lifespan of mining machinery, reducing the need for frequent replacements.
5. Improving Operational Efficiency – Well-lubricated equipment operates more smoothly and efficiently, consuming less fuel and power. This not only enhances performance but also lowers operating costs in the long run.
Key Mining Equipment Components That Require Lubrication
Mining equipment contains many critical components that rely on lubrication to function properly. Some of the most important areas include:
- Bearings & Bushings – Essential for keeping crushers, screens, and conveyor belts running smoothly.
- Hydraulic Systems – Found in excavators, loaders, and drills, hydraulic fluid is crucial for smooth and precise operation.
- Gearboxes & Transmissions – Heavy machinery requires constant lubrication to maintain smooth gear shifting and reduce mechanical stress.
- Chains & Cables – Draglines and shovels use chains and cables that need lubrication to prevent rust and snapping.
- Tracks & Undercarriage Components – Tracked equipment like bulldozers and excavators need frequent greasing to reduce wear and maintain mobility.
Selecting the Right Lubricant for Your Equipment
Not all lubricants are created equal. Choosing the wrong one can result in poor performance, increased wear, and equipment failure. Consider these key factors:
Viscosity – The right lubricant should have the correct thickness (viscosity) to provide adequate protection without slowing down machinery.
Extreme Pressure (EP) Properties – For mining equipment that handles heavy loads and high impact, lubricants with EP additives are essential to prevent wear under pressure.
Water Resistance – Since mining environments often expose equipment to water and mud, lubricants should have high water resistance to prevent washing away.
Temperature Stability – Mining operations often experience extreme heat and cold. A good lubricant must remain stable across a wide temperature range.
Best Practices for Lubricating Mining Equipment
Applying lubrication correctly is just as important as choosing the right type. Follow these best practices to ensure maximum equipment longevity and performance:
1. Follow Manufacturer Recommendations – Each piece of mining equipment has specific lubrication needs. Always use the manufacturer’s recommended lubricant type and application schedule to avoid issues.
2. Use Automated Lubrication Systems – Modern mining operations use centralized lubrication systems that apply lubricants consistently and precisely, reducing manual labor and eliminating human error.
3. Monitor Lubricant Condition – Regular oil analysis and lubricant testing help detect contamination, viscosity breakdown, and wear particles before they lead to equipment failure.
4. Keep Lubricants Clean and Contaminant-Free – Store lubricants properly in sealed containers to prevent contamination from dust, dirt, and moisture.
5. Train Your Maintenance Team – Operators and technicians should be well-trained in proper lubrication techniques to ensure best practices are followed consistently.
The Cost of Neglecting Lubrication
Ignoring lubrication can have serious consequences for mining operations. Some of the risks include:
Increased Equipment Downtime – Lack of lubrication leads to premature wear and frequent breakdowns.
Higher Repair Costs – Replacing worn-out parts due to poor lubrication is far more expensive than regular maintenance.
Reduced Productivity – Downtime means lost production hours, leading to decreased output and revenue.
Higher Fuel Consumption – Poorly lubricated machines require more energy to operate, increasing fuel costs.
Lubrication is not just another maintenance task—it’s a crucial factor in keeping mining equipment running efficiently. Proper lubrication reduces wear, prevents breakdowns, improves efficiency, and extends equipment lifespan.
At Rackers Equipment Company, we understand the importance of high-quality, well-maintained equipment. Whether you need new or used mining machinery, expert advice, or maintenance tips, we’re here to help.
Contact us today at 573-635-8700 to learn more about our heavy equipment solutions and keep your mining operation running smoothly!